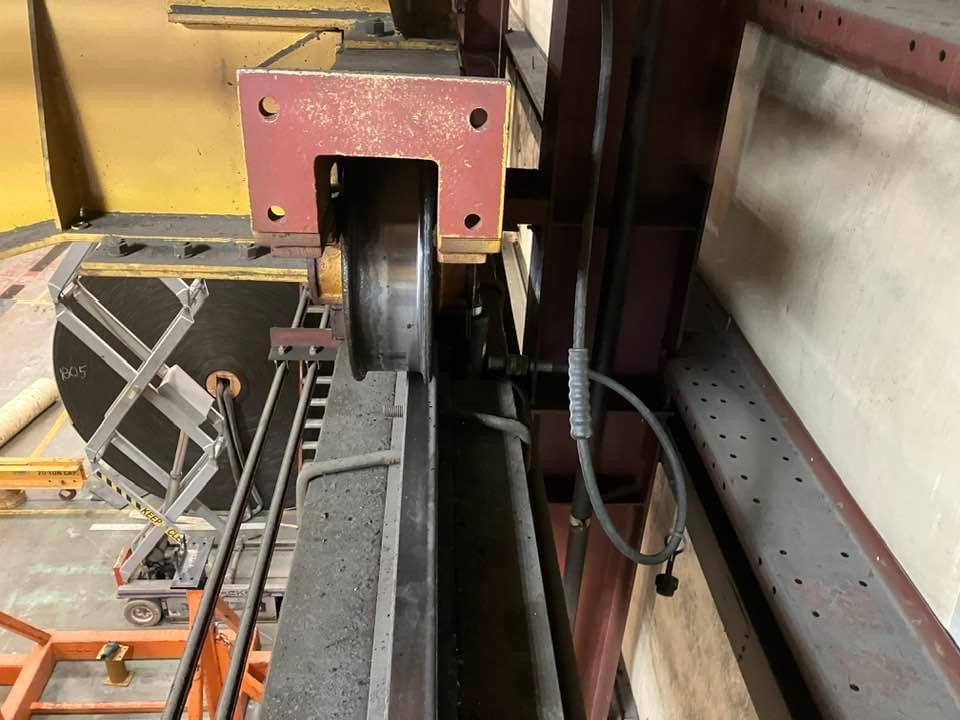
Premature Wear Leads to Discovery of Contract Breach for Sale of New Overhead Cranes
A few years back in one of our first expert witness engagements, we were subcontracted to another expert witness in the field that was examining reasons for premature wear and excessive warranty claims. A quick analysis by our team discovered that many features of the cranes did not meet the technical terms on the proposal. Instead of supplying the more expensive features promised, the crane company chose to supply less expensive features typically found on a crane designed for lighter-duty applications. Our team was able to examine the duty cycle design guidelines in the Crane Manufacturer’s Association of America specification 70 and make a clear picture of just how diminished the capabilities of the cranes supplied were as compared to the promises made at the time of sale.
Our team also found that the runway endstops were missing and instead the crane company painted oxide red squares on the white wall at the end of the runway.
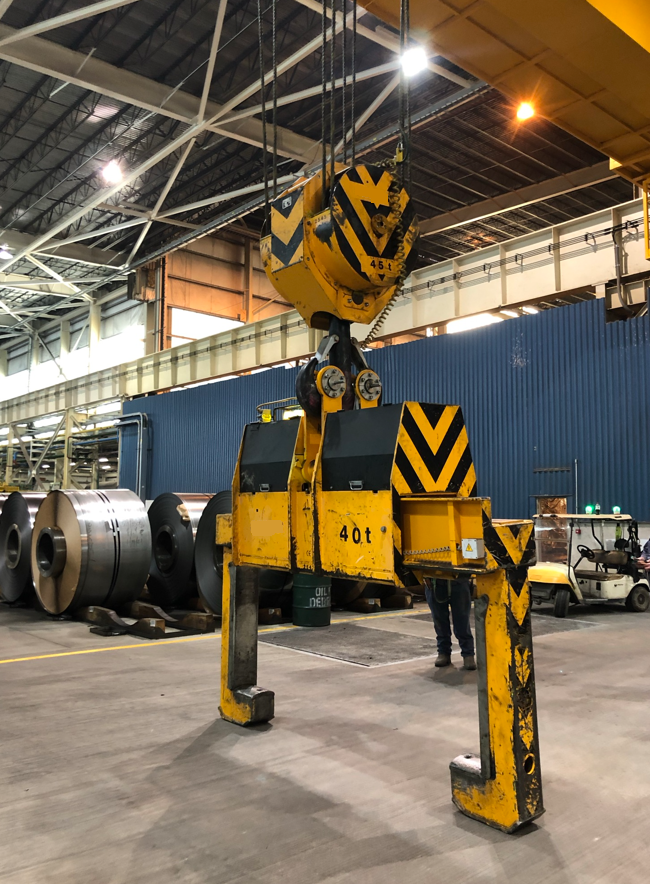
Automation-Ready Coil Grabs for Major Auto Manufacturer
While steel mills and container ports see frequent crane automation, the trend is moving down-market to medium-heavy duty cranes found in places like steel coil warehousing applications. Because the overhead cranes in these places are typically priced at half or less of a steel mill overhead crane, it is important to find areas of eficiency. Our team came together with major end-users of overhead cranes and the leading automation company to come up with a bill of materials for an “automation-ready” coil lifter that has all of the sensors and IOT devices necessary to successfully automate a coil grab without intensive back-and-forth work involving the mechanical design team and the automation design team. This was done in response to a prior project where the design and integration process took months longer than it should have.
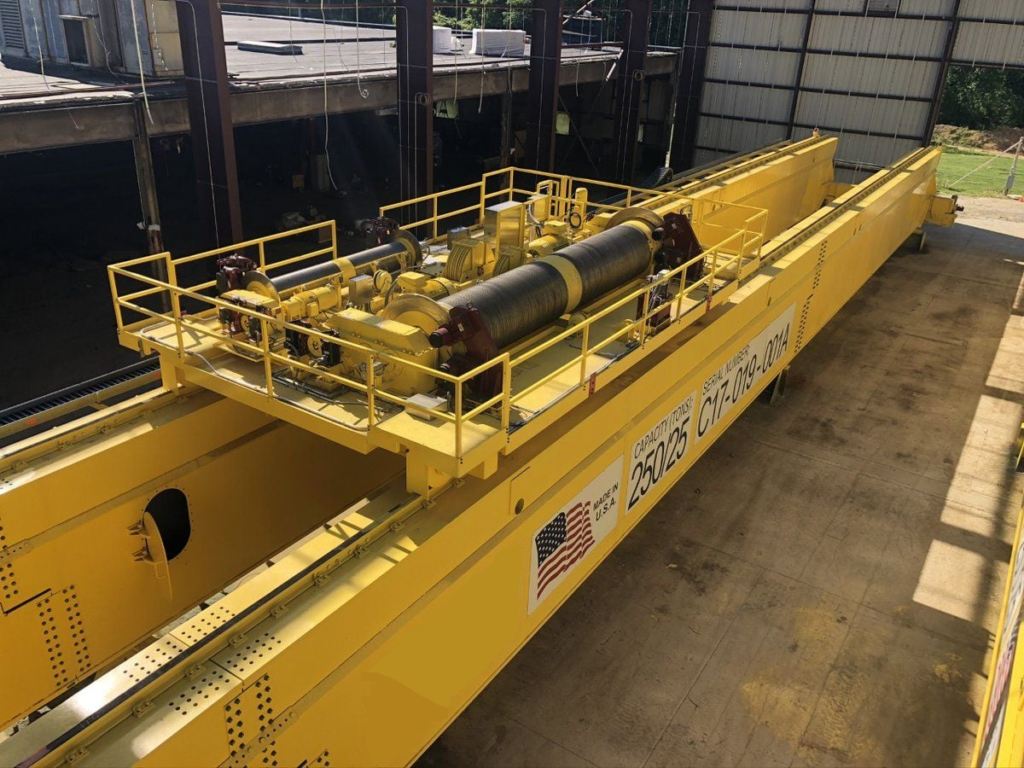
Two Weeks to Figure out my Biggest Crane Sale
Around 2017, I was contacted by our home office when I worked for another crane manufacturer. The EVP that I reported to asked me if I could help estimate the sale price of (5) extremely complex overhead cranes built to NASA standards. For those not familiar with overhead cranes built to NASA standards, that means lots of extra features designed to prevent damage or loss to extremely valuable loads such as aircraft or spacecraft. Typically overhead cranes are designed to protect the users and operators. In this case each crane was furnished with multiple electric wire rope hoists that featured extra brakes on both the motor side and drum side to prevent load drops in case of broken driveshafts and couplings. The hoists also featured redundant wire rope reeving, which means one rope could break and run completely off the hoist and crane, while the other rope would safely hold the load.
When the cranes were delivered, the two largest cranes ultimately featured CMAA Class D design criteria (heavier duty than average), 200 foot spans, and a 250 short ton main hoist. In order to fit down the highway safely, each girder was made in three parts. We were able to produce a competent proposal for five very large overhead cranes in a record two weeks mostly becuase we had a team of highly experienced people that could use their long-term knowledge to contribute completed parcels of information such as costs, weights, and dimensions rather than starting from scratch. In particular, Tad’s historic data records were able to come up with a trolley-hoist weight within five percent of the actual value which allowed the structural team to start work concurrent with the electrical and mechanical team rather than waiting for the mechanical team to finish.